3D printed composite elastic fabric
Instructor:Jenny Sabin
This study is part of my thesis research, which aims to build tangible interactive interfaces through materials research.
This study obtained self-fold results on pre-stretched fabrics by 3D printing, so this part mainly shows the results of material research and the attempt at digital fabrication for manufacturing products.
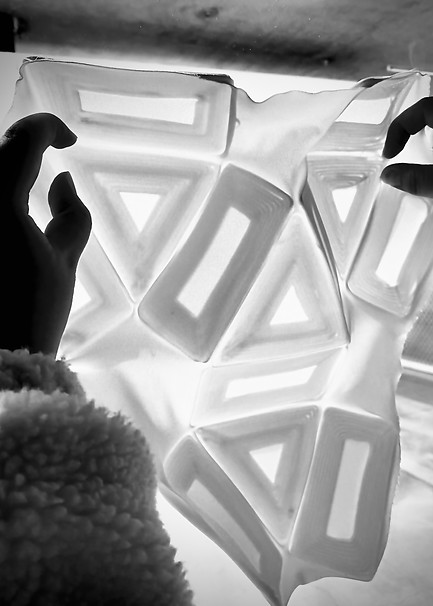

Based on the 3d printing end effector we have conducted a series of self-folded material studies.
Material experiments: gap distance, printing thickness, printing material (pla, tpu), living hinge design.




.png)
Although the material test has achieved the desired effect, the printing size of most 3D printers on the market is about 20cm*20cm, which is not enough to complete the fabrication of large-scale interfaces.
Therefore, using the robotic arm as a tool for 3D printing creates possibilities for the fabrication of large-scale interactive interfaces.
However, most of the 3d print extruders on the market that robot arms can use cost around $2000+, far beyond the budget.
Therefore, how to manufacture an affordable 3d print end effector has become a problem to be solved.
A specific understanding of 3d printers is required. In order to make a 3d print end effector, one must first understand the structure of a DIY 3d printer.
In order to complete the end effector with 3d printing function:
-
Debug the machine;
-
hacked operation system
-
Synchronize data between end effector and robot arm
This research has laid the foundation for the subsequent manufacture of material robots, and fabrics, as a kind of smart material, also have a great possibility to be embedded in various sensors and actuators to respond to environmental information.